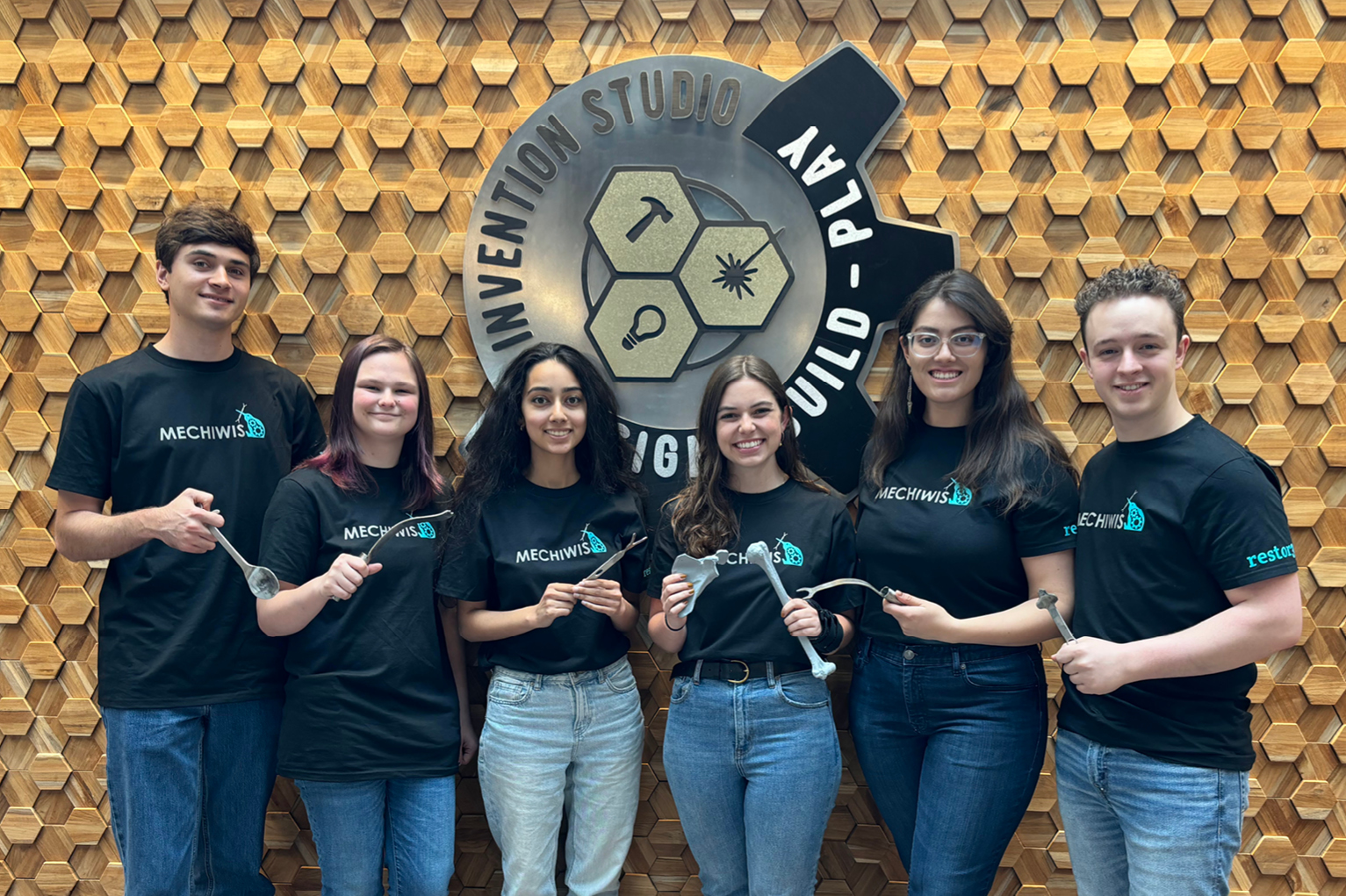
Meet Capstone Design Team Mechiwis
April 17, 2024
By Ashley Ritchie
Get to know mechanical engineering Capstone Design team Mechiwis who is redesigning retractors for total shoulder replacement surgeries, to improve ergonomics and shoulder joint access, for the Spring 2024 Georgia Tech Capstone Design Expo. The team's sponsor is restor3d and they are advised by Director of Design & Innovation Amit S. Jariwala.
1. Can you tell us about your team and project?
We are team Mechiwis, a team of mechanical engineering majors and Invention Studio PIs that are all extremely involved in the space. We all have a passion for the studio and prototyping, which is why we chose this project. This may seem like a biological sciences problem, but we determined that at its core it is a prototyping project.
We are redesigning retractors for total shoulder replacement surgeries, to improve ergonomics and shoulder joint access. Retractors are tools used in the operating room to maneuver muscle tissue and bone to give the surgeon better access to the problem. Our retractors will help surgeons make surgeries quicker and easier, in the long-term improving patient outcomes and reducing costs.
Team members include:
- Miguel Daly – Jacksonville, Florida
- Max Gart – Avon, Connecticut
- Isabelle Gustafson – Carrollton, Georgia
- Sana Hafeez – Duluth, Georgia
- Lena Moller – Flowery Branch, Georgia
- Claudia Vitale – Tampa Florida
2. What is your team’s design process, how do you go about separating different tasks, and what are some of the biggest challenges you have faced?
The first step in our design process was to understand the surgery and the current market challenges, which we did through online research and surveying shoulder surgeons. We moved on to ideation, with some simple sketches that were shown to the sponsor for feedback. Our team’s strength is fabrication, so we started prototyping as fast as possible. The first versions were bent pieces of waterjet sheet metal, and eventually the material chosen got so tough to bend that it had to be forged. Physical iteration was key here, so there was a lot of shipping prototypes back and forth to the sponsor. Each iteration received feedback from the sponsor and an expert surgeon, and a new version was made with that in mind. Eventually we landed on the current set, made of waterjet and forged 17-4 PH stainless steel. This set has been tested by us in two cadaver labs and evaluated by the expert surgeon. Since we received all positive feedback from this and they fit all the requirements on our specification sheet, it's the final set!
Our biggest challenge was definitely being an all mechanical engineering team working on a biomedical project. We had no idea if we were going to be too squeamish to watch the surgery videos or do the testing. Also, since most of us have no biology background, we didn’t know if we would be able to learn enough to do this project in a semester. In the end, everything worked out and after playing to our strengths as a team, we’ve come up with a product we’re proud of!
3. Have there been any highlights while working on your project?
In early April, we drove to our sponsor’s facility in North Carolina and were able to test our retractors’ performance in a real cadaver lab. Two of our members actually got to assist the surgeon during the procedure, which was a really unique experience. We used the information from that lab to further refine our tools and completed a second cadaver lab in the Atlanta area thanks to the support we have received from the Capstone Design program. One of the other highlights was our manufacturing process for the last set of retractors. They are made from such a hard stainless steel that they can’t be bent by traditional sheet metal breaks, so they had to be heated to red hot and then hammered into the correct shape. We learned a little blacksmithing!
4. Can you tell us about your experience working with a sponsor?
Honestly, our sponsor has been great. The team at restor3d has been extremely helpful throughout the entire process and enthusiastically supportive towards our ideas. Being able to have knowledgeable industry professionals weigh in and provide feedback has been an invaluable resource. We had a great time when we went to visit and tour their manufacturing facility!
5. If you could go back in time, what advice or message would you give your team on day one?
For us, the best thing to do was to start trying. We learned just as much from our successes as our failures. The designs that didn’t work out pointed us in the direction we needed and helped us make a better product. We would tell our past selves to not be afraid to ask questions, because every single question has a benefit.
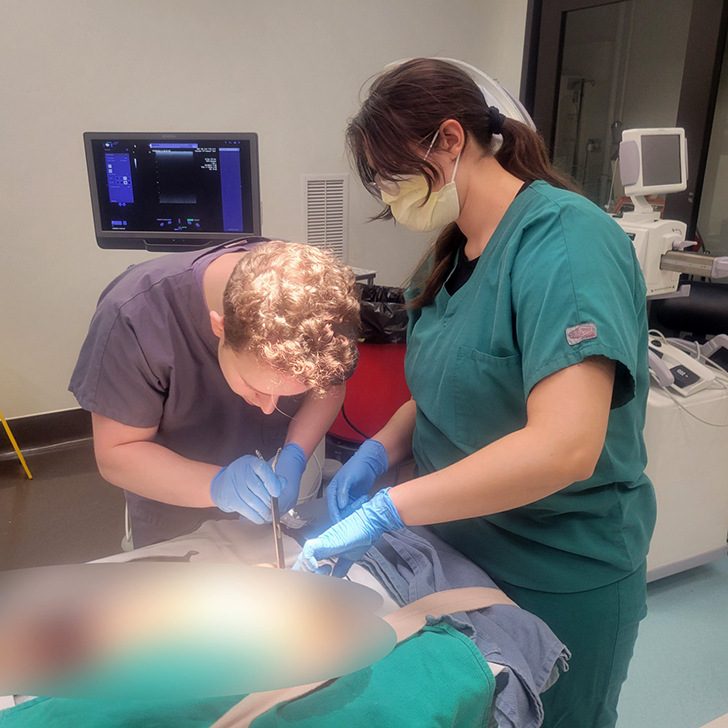
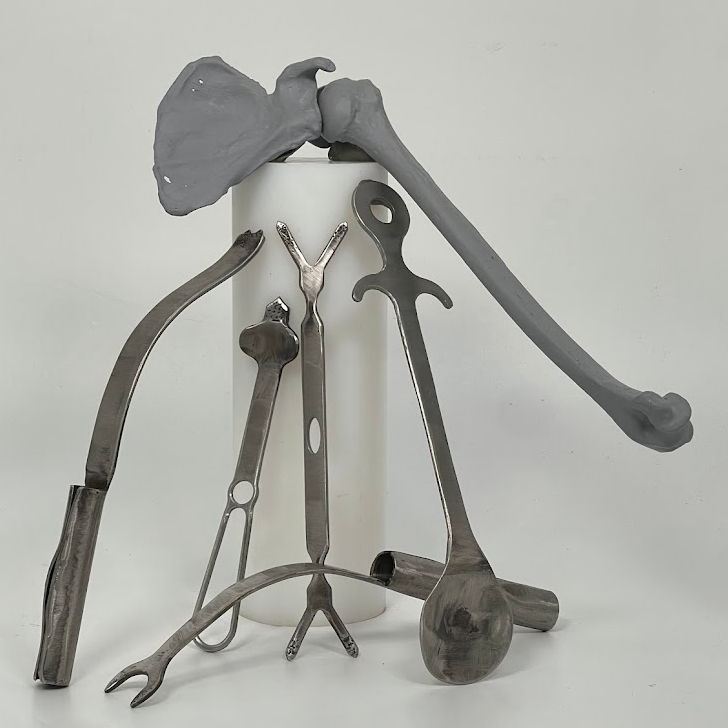
The Spring 2024 Georgia Tech Capstone Design Expo will be held on Tuesday, April 23, at McCamish Pavilion on the Georgia Tech campus. At the Expo, over 1200 seniors from various disciplines of engineering, sciences, public policy, and industrial design will showcase their innovative projects designed and built during their Senior/Capstone Design course. Register to attend here!
This semester's Expo includes over 70 industry sponsors. Their donations support Transforming Tomorrow: The Campaign for Georgia Tech.